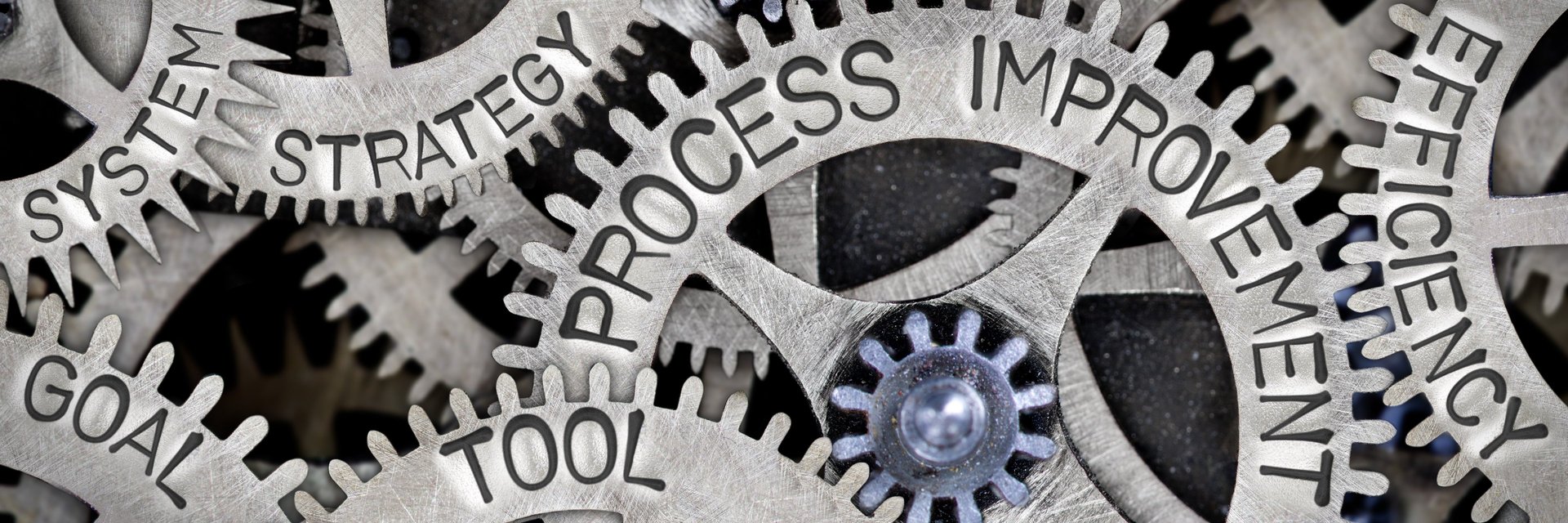
Process Improvement Solutions for
Small Business
Common Small Business Challenges
· Work Flow Inefficiencies
· Systems Inefficiencies
· Lack of Proper Software or Applications
· Purchasing Issues
- Inventory Costs
- Supply Costs
- Inbound/Outbound Freight
· Lack of Process Visibility
· Bottlenecks
· Redundancy or Duplication of Work
· Quality Control Issues
· Integration Issues
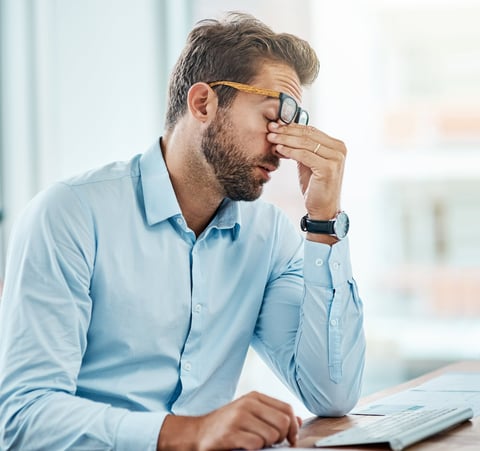
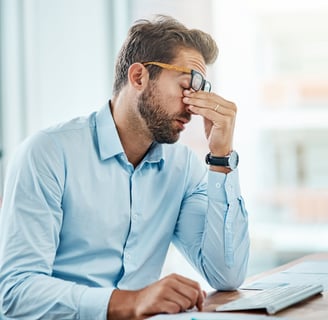
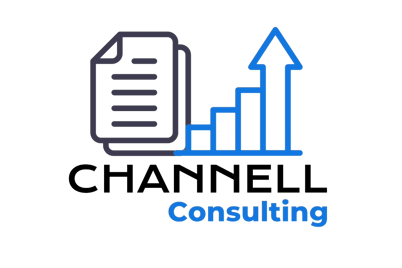
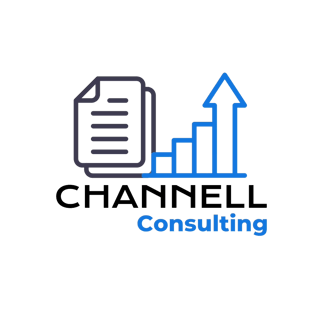

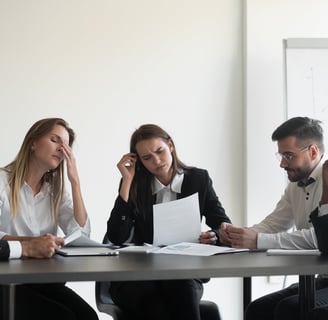
Services Offered for Small Business
· Streamline processes using Lean Process Improvement
· Reduction in Freight Costs
· Better Inventory Management
· Improved Purchasing and Finance
· Document Creation, Review and Updates
- Policies
- Procedures
- Work Instructions
· Data Analytics
· Automated Excel Spreadsheets
· Customized Access Software
· Software Implementation
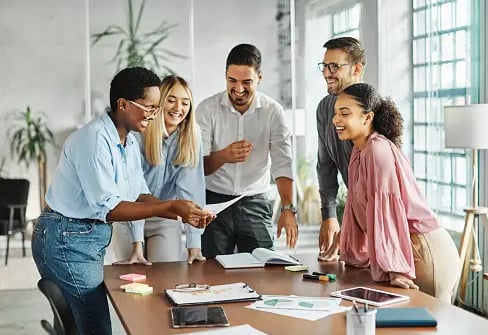
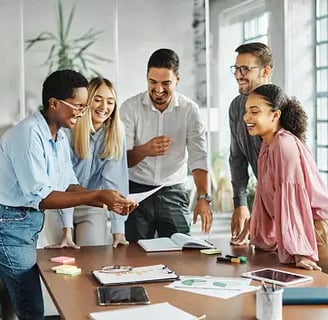
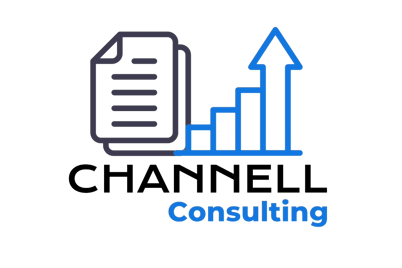
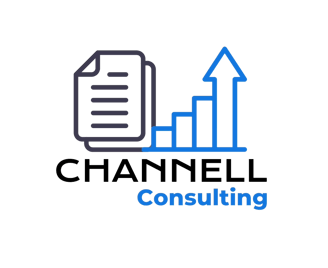
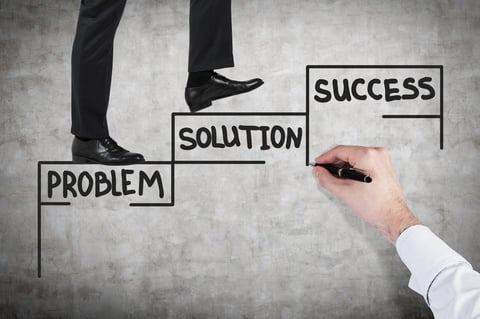
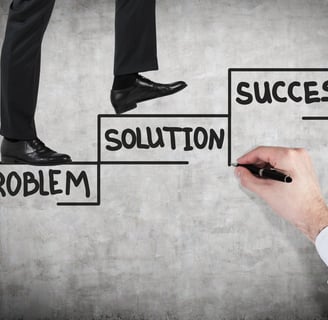
Why Small Business?
Large and even some medium sized companies have engineers or employees dedicated to process improvement. Many times, smaller businesses can’t justify a full-time employee for process improvement or may not need a full-time person. That is where Charles comes in to provide his services that can improve your business in many of these areas and more.
· Warehousing Efficiency
· Manufacturing
· Freight Costs
· Quality
· Safety
· Purchasing
· Inventory
· Accounts Payables
· Accounts Receivables
· Cash Flow Management
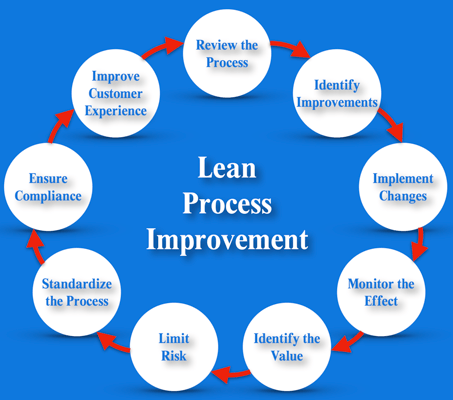
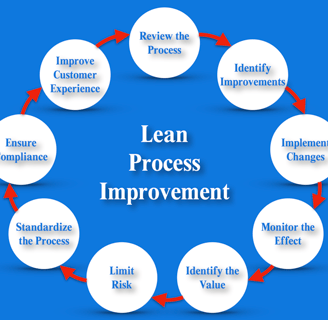
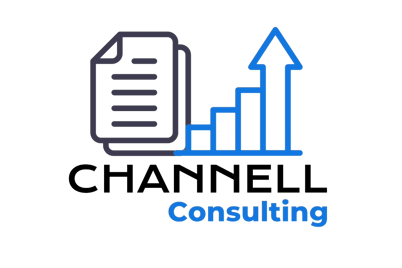
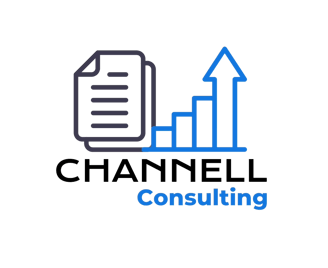
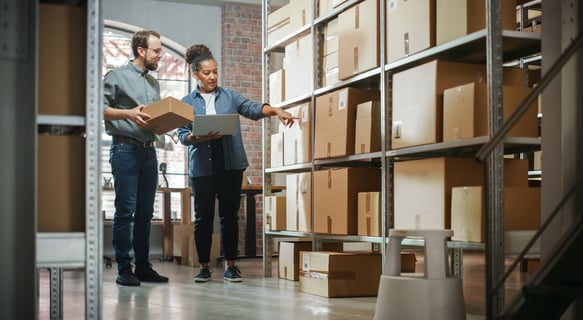
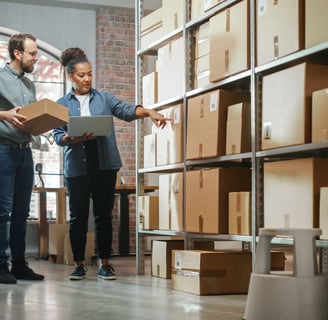
Process improvement is a truly crucial aspect of organizational development that contributes to efficiency, effectiveness and adaptability. It helps small businesses stay competitive, respond to changes in the business environment and deliver value to customers and stakeholders. See some of the many benefits below.
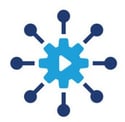
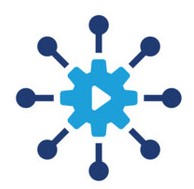
Customer Satisfaction
Increased Productivity
Improved Employee Morale
Streamlined and improved processes often lead to better products or services, meeting or exceeding customer expectations and ultimately enhancing satisfaction.
Efficient processes and workflows enable teams to accomplish more in less time, boosting overall productivity and allowing organizations to handle increased workloads.
Employees often find satisfaction in working with well-defined and efficient processes. Streamlining workflows can reduce frustration, enhance job satisfaction, and contribute to a positive work culture.
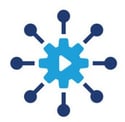
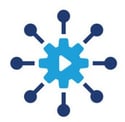
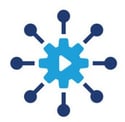
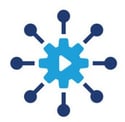
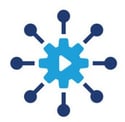
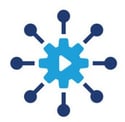
Increased Efficiency
Streamlining processes eliminates unnecessary steps and reduces bottlenecks, leading to quicker task completion and overall efficiency gains.
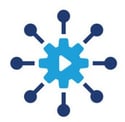
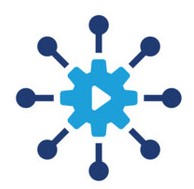
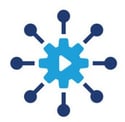
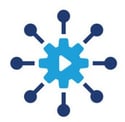
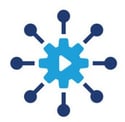
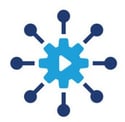
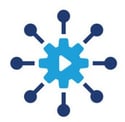
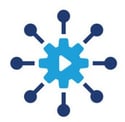
Cost Reduction
Enhanced Quality
Innovation and Agility
Risk Reduction
Improved processes often result in resource savings, such as reduced time, materials, or labor costs, contributing to overall cost-effectiveness.
By identifying and eliminating errors or defects in processes, the quality of the final output or product is enhanced, leading to increased customer satisfaction.
Continuous process improvement encourages a culture of innovation. Teams that regularly evaluate and refine processes are more adaptable and better positioned to respond to changes in the business environment.
A well-defined and optimized process often includes built-in checks and balances, reducing the likelihood of errors, compliance issues and other risks.
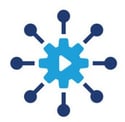
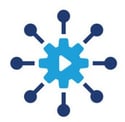
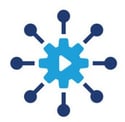
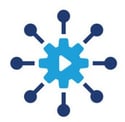
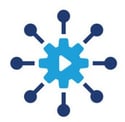
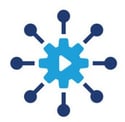
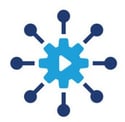
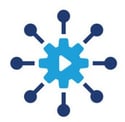
Data-Driven Decision-Making
Process improvement relies on data analysis to identify areas for enhancement. This data-driven approach facilitates informed decision-making and helps organizations prioritize improvements based on measurable metrics.
Response to Market Changes
Organizations with efficient processes can adapt more quickly to changes in the market, technology, or customer demands, giving them a competitive edge.
Compliance and Regulation
Adhering to standardized and optimized processes can help organizations meet industry regulations and compliance standards, reducing the risk of legal issues.
Consistency & Standardization
Standardized processes ensure consistency in outputs, making it easier to maintain quality and reliability across different teams or locations.
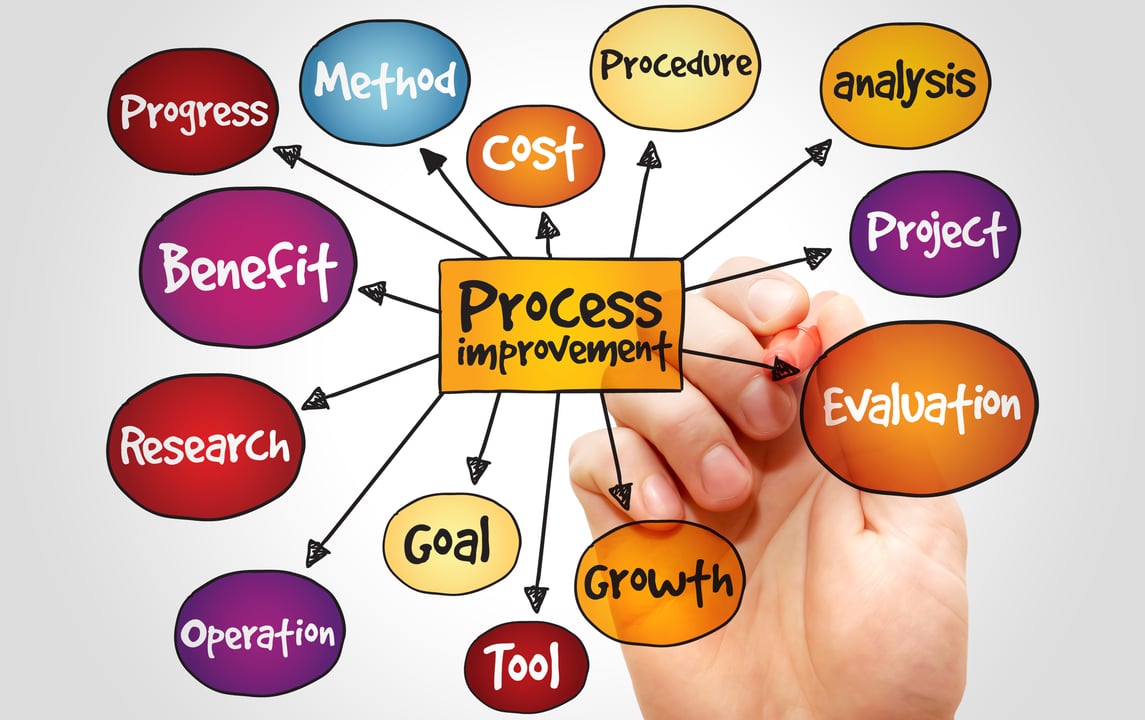
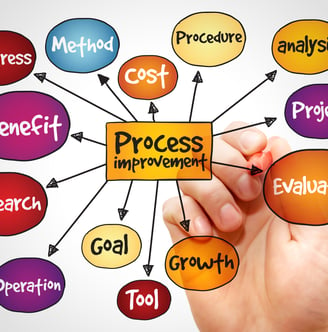
About Charles
Charles Channell started as an Industrial Engineer and continued to grow through further business education and management experience for the past 35 years. He has degrees in engineering and business, a Six-Sigma certification and is a certified Project Management Professional (PMP) with experience in process improvement, software development & implementation, operations management, and maintaining ISO/QS9000 standards. While overseeing distribution engineering for a Fortune 500 company and as CEO of a 3PL Logistics company, his primary goal was to improve processes and quality of operations while cutting costs.
Over the past 10 years, he managed finances for a global logistics company and served as Project Manager for software implementation.
PMP Certified Project Manager
Professional Engineer
Software Developer
MS Office Expert - Access/Excel
Six Sigma Certified
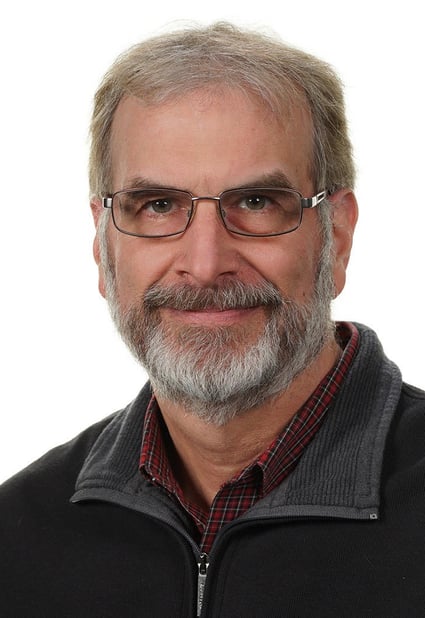
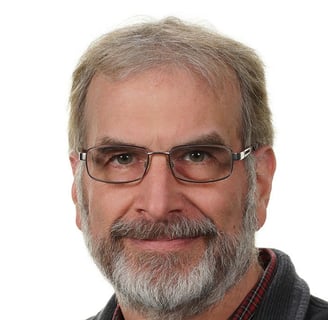
Located in Lebanon, TN Charles provides services to Wilson County and it's surrounding counties.
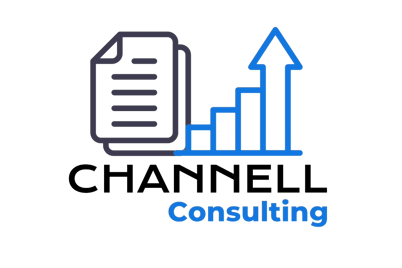
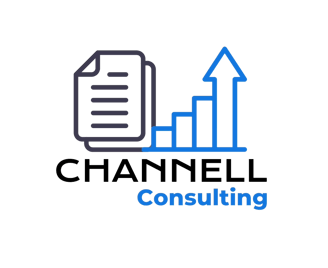
Customer Reviews
"Charles has been instrumental in streamlining our operations, resulting in increased efficiency and cost savings"
"Working with Charles has been a game-changer for our business. His process improvement strategies have transformed our operations and improved our bottom line"
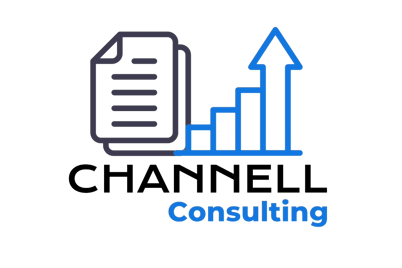
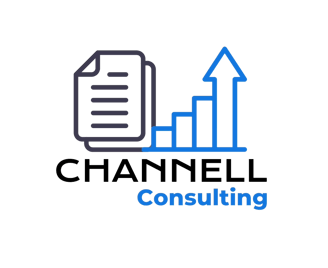
Channell Consulting
Lebanon, Tennessee
Email: charles@channell-consulting.com
Phone: (615) 521-4657